5th March 2023
Media coverage - North American Mining Magazine features Centre-developed coarseAIR as a new & innovative new technology
Innovation in mineral processing
February 26, 2023 Jonathan Rowland
Coarse particle flotation and bulk ore sorting are starting to make waves in the mineral processing industry. North American Mining takes a look at both technologies with the help of experts from three leading mineral processing OEMs.
By Jonathan Rowland
Innovation in mineral processing — North American Mining Magazine
–
Extract: CPF IN ACTION: FLSMIDTH COARSEAIR
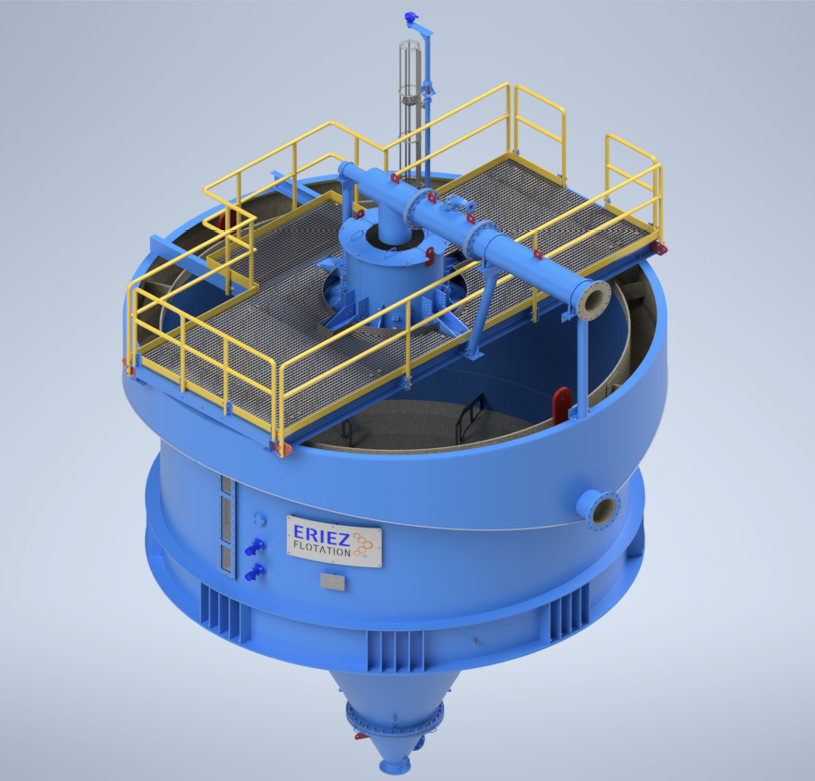
FLSmidth is another company working to establish CPF as an accepted technologies within mineral processing. Its coarseAIR technology is “essentially a fluidised bed separator to an up-current classifier,” explained the company’s flotation point man, Lance Christodoulou.
“Coarse particles are presented without the agitation or mixing in the cell that you have in conventional flotation. As a result, bubble particle detachment is reduced. Meanwhile, the fluidized bed generates a semi-permeable layer, which prevents penetration of particles attached to bubbles. These particles are instead taken with the up-current to the lamella region, where there can be extracted. The lamella region also serves to reject any hydraulically misplaced particles: particles that are not attached to bubbles but are hydraulically carried into the lamella region, are rejected back into the separator. This provides a very high-grade concentrate, relatively speaking, for coarse particles.”
According to Christodoulou, there is increasing interest from the mining industry in CPF. FLSmidth itself is doing significant pilot work to demonstrate the capabilities of coarseAIR in its laboratory and onsite. The company has also recently received a grant from EIT Raw Materials to look at upscaling the coarseAIR technology. That project is due to kick off in 2023.
“I think it’s currently something that’s definitely being considered at existing mines,” said Christodoulou, who also emphasised the potential for the technology to treat tailings. “The low hanging fruit is to use CPF to treat the tailing stream. There’s a huge potential market out there for installing these modules to go after the coarse fraction of material that’s currently being lost. But as these circuits get implemented and adopted, I think you’ll start seeing implementation in the front-end of the circuits – so in a rougher-type flotation environment. And once the technologies and the fundamental approach is proven out in that part of the circuit, you’ll start to see the technology implemented in from the outset at greenfield applications.”
When it comes to installing the coarseAIR at a brownfield site, “a new circuit would have to be built,” continued Christodoulou. “Two options are to put it on the tailings stream to treat material coming from the plant to the tailings impoundment, or to put it within the circuit itself. That would require installing some cycloning to produce a coarse stream and a fine stream. The fine stream would go to the conventional flotation, and the coarse portion would go to the coarseAIR module, comprising a coarseAIR and dewatering cyclones, as well as dewatering systems for the underflow.”
Christodoulou also noted the potential for CPF to improve tailings management. “The tailings from coarse flotation is very easily dewatered. Water recovery is therefore fairly quick, and water losses in the circuit are reduced because significantly less water is sent to the tailings impoundment. Alternative dewatering techniques, such as horizontal belt filters or similar, can be used recover water quickly and produce a fairly dry, stackable material for de-comingled tailings or dry stack tailings.”